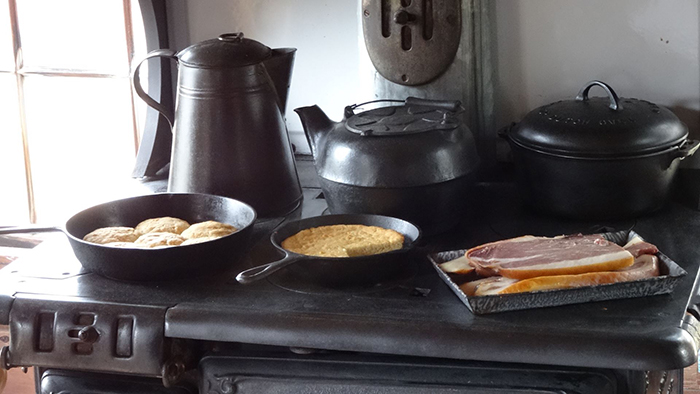
All 10 formulas a from a historic, archived document: do not assume content reflects current scientific knowledge, policies, or practices.
The following formula gives a liquid stove blacking:
1.
Graphite in fine powder, 1 lb.;
lampblack, 1 oz.;
rosin, 4 oz.;
turpentine, 1 gal.
This form may be esteemed a convenience by some, but the rosin will, of course, give rise to some disagreeable odor on first heating the stove, after the liquid is applied.
The mixture must be kept well shaken while in use, and must not be applied when there is a fire or light near on account of the inflammability of the vapor.
The solid cakes of polish are said to be made by subjecting the powdered graphite, mixed with spirit of turpentine, to great pressure. It has to be reduced to powder and mixed with water before being applied.
Any of them has to be well rubbed with a brush after application to give a handsome polish.-—from the Druggist Circular, circa 1900.
2.
A correspondent of The Pharmaceutical Era [c. 1900] submits the following formula for a preparation which lie says his company advertises as a “dustless paste stove polish:”
Animal charcoal, 8 parts;
blacklead, 8 parts;
molasses, 4 parts;
sulphuric acid, 2 parts;
hydrochloric acid, 1 part;
water, enough to make a paste.
He says he allows the acids to act on the charcoal and molasses for twenty-four hours, after which the graphite is added with enough water to form a paste.
He says that the trouble with this paste is that “it forms a layer on the cloth when applied, and this layer in contact with a warm stove falls as dust to the floor.”
The French stove polish which is used for blackening and polishing iron stoves is produced in the following manner:
3.
Turpentine oil, French or American, 23’0 kilos.:
American lampblack, 3’0 kilos.;
prime black, fat, finely elutriated graphite, 2’0 kilos.
4.
Ceresine, 3’0 kilos.; carnuba wax, 0’5 kilo.
Melt the ceresine and carnauba wax in a tinned or enameled kettle over a moderate fire and add mixture 3, previously stirred cold, to the fusion. 4, but only at a distance from the fire, with stirring.
Pour this mixture through a fine metal sieve into a second vessel, and next, for a more intimate mixture, from one kettle into another until it begins to thicken, and only then fill into tin cans.
If the paste should have become a little too cold during the filling of the tins, so that it interferes with the pouring, all that is necessary is to put the vessel into a larger one containing boiling water, whereby it is rendered more liquid again.—-from Scifensieder Zeitung, circa 1900.
5.
Ceresine…. 120 grams.
Japanese vegetable wax…. 100 grams.
Turpentine oil…. 1,000 grams.
Fine lampblack…. 120 grams.
Graphite…. 100 grams.
Unite ceresine and wax by melting, add to the half cooled, liquid mass the lampblack and graphite ground in the oil of turpentine and stir until completely cool.—from Farben Zeitung, circa 1900.
6.
For a liquid stove polish try the following:
Copperas…. 10 parts.
Boneblack…. 5 parts.
Graphite, in powder…. 5 parts.
Water sufficient to make a paste. The addition of a small amount of alum to this is said to improve it.
Another cheaper formula is as follows:
Soap, common yellow…. 10 parts.
Resin, in powder…. 5 parts.
Water, sufficient
Boneblack or plumbago, sufficient. Mix the resin and the soap (the latter finely shaved), add 40 parts of boiling water and heat until a homogeneous mixture is obtained.
Stir in the blacking material and remove from the fire. Test a small portion, and then dilute with boiling water to suit.
7.
If cost is no object, the following will prove all that can be desired:
Bayberry wax…. 10 parts.
Plumbago, in fine powder…. 200 parts.
Coal oil, sufficient.
Melt the mineral wax with a portion of the oil over a water bath, and pour the product into the rest of the oil, stirring well. Grind up the plumbago with the product, adding a little at a time, until you arrive at the desired consistency.—-from National Druggist, circa 1900.
Paste Stove Polish.—
8.
Plumbago…. 2 lb.
Water…. 8 oz.
Turpentine…. 8 oz.
Sugar… 2 oz.
Knead thoroughly and keep in tin boxes. Apply with a brush.
Here are several other formulas:
9.
Mix:
2 parts of black-lead,
4 parts of copperas, and 2 parts of boneblack,
with water, so as to form a creamy paste.
This is an excellent polish, as the copperas produces a jet black enamel, causing the black lead to adhere to the iron.
10. Moisten plumbago with turpentine in which resin has been dissolved, to make it adhesive, and subject it to strong pressure in appropriate moulds.–from Pharmaceutical Era, circa 1900.